Papier przeszedł długą drogę, zanim zaczął być wytwarzany w takiej formie, w jakiej go obecnie znamy. Wynaleziony w Chinach, od samego początku stanowił ważny nośnik informacji, a do jego wytwarzania były wykorzystywane włókna jedwabne i lniane.
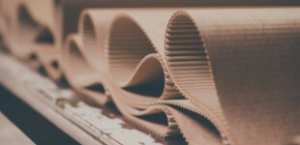
Surowce i dodatki chemiczne do produkcji papieru
Proces produkcji papieru składa się z kilku etapów. Pierwszy z nich polega na rozdrobnieniu i oczyszczeniu masy włóknistej, która może być pochodzenia pierwotnego (drewno) lub wtórnego (makulatura). Głównym źródłem włókien celulozowych jest drewno otrzymywane w tartakach pod kilkoma postaciami, np. jako kłody, wióry czy też trociny.
W kolejnym etapie materiał włóknisty podlega dalszej obróbce, gdzie przekształca się go w miazgę (pulpę), a tę z kolei przetwarza się w papier. Wytwarzanie pulpy może się odbywać metodami mechanicznymi lub chemicznymi. W procesie roztwarzania chemicznego wykorzystuje się zazwyczaj alkalia (np. wodorotlenek sodu w postaci ługu lub też sodę kaustyczną), które mają na celu usunięcie ligniny spajającej włókna.
Kluczowym jest także zastosowanie preparatów odpieniających na każdym etapie produkcji samego papieru. Substancje odpieniające stosuje się w procesie wytwarzania wszystkich rodzajów wyrobów papierniczych. Piana powstaje w wyniku mieszania gazów z masą celulozową i jest w niej zatrzymywana na skutek obecności środków powierzchniowo-czynnych. Do usuwania piany powstającej w kolejnych etapach produkcji papieru z powodzeniem mogą być stosowane produkty znajdujące się w ofercie Grupy PCC. Należą do nich kopolimery blokowe EO/PO o nazwie ROKAmer oraz seria alkoksylowanych alkoholi tłuszczowych (ROKAnole LP). Ich wysoka skuteczność w likwidowaniu piany oraz w zapobieganiu jej powstawania umożliwia poprawę wydajności kolejnych etapów technologicznych.
Metody chemiczne roztwarzania włókien
Metody chemiczne roztwarzania włókien polegają głównie na stosowaniu różnych reagentów chemicznych, a także na dostarczaniu ciepła w celu zmiękczenia ligniny. W wyniku ich działania środków chemicznych dochodzi do jej rozpuszczenia, a następnie do mechanicznej rafinacji prowadzącej do oddzielenia włókien. W praktyce stosowane są dwa różne procesy roztwarzania chemicznego.
Pierwszym z nich jest proces roztwarzania siarczanowego, potocznie nazywany procesem Krafta. Obecnie jest to dominująca technologia. Dzięki jej stosowaniu przetwarza się około 80% światowej produkcji masy celulozowej. Roztwarzanie Krafta stało się najczęściej wykorzystywaną metodą ze względu na kilka czynników. Włókna po roztwarzaniu siarczanowym charakteryzują się lepszą wytrzymałością w porównaniu do uzyskanych w wyniku innych dostępnych technologii. Dodatkowo może być ono stosowane do wszystkich gatunków drewna, a sam proces umożliwia skuteczne odzyskiwanie zastosowanych surowców chemicznych.
Metoda Krafta polega na łączeniu zrębków drewnianych z ługiem białym (jest to wodny roztwór wodorotlenku sodu i siarczku sodu). W warunkach podwyższonego ciśnienia i temperatury roztwór ten rozpuszcza ligninę, uwalniając włókna celulozowe. Po skończonej reakcji trawienia uzyskujemy czarny ług i masę celulozową. Ług zawiera rozpuszczone substancje organiczne, które są odzyskiwane i mogą być wykorzystane w ponownym procesie roztwarzania chemicznego. Natomiast z uzyskanej masy (w obecności tlenu i wodorotlenku sodu) usuwa się ligninę w procesie delignifikacji tlenowej. Otrzymany w taki sposób materiał jest bielony w celu uzyskania odpowiednich właściwości użytkowych, takich jak wytrzymałość, jasność i czystość końcowego produktu.
Drugim z procesów chemicznego roztwarzania jest proces siarczynowy. Polega on na zastosowaniu wodnego roztworu ditlenku siarki w obecności zasad (np. wapniowej, magnezowej, sodowej i amonowej). Uzyskiwane w tym procesie produkty są jaśniejsze i łatwiejsze do wybielenia, jednak posiadają one zdecydowanie niższą wytrzymałość w porównaniu do częściej stosowanego roztwarzania siarczanowego. Roztwarzanie siarczynowe wymaga także starannego doboru surowca drzewnego – metoda ta jest nietolerancyjna np. dla drewna sosnowego. Proces siarczynowy w porównaniu z metodą Krafta wytwarza mniej nieprzyjemnych gazów, charakteryzuje się większą wydajnością, a także pozwalana na uzyskanie bardzo jasnej pulpy, którą łatwo się ługuje. Niestety, ze względu na słabszą jakość włókien, wyższe zużycie energii i niskie zdolności odzyskiwania zastosowanych w procesie surowców chemicznych, technologia siarczynowa została wyparta przez proces Krafta.
Metody mechaniczne roztwarzania włókien
Roztwarzanie mechaniczne pozwala uzyskać bardzo wysoką wydajność pozyskiwania mas włóknistych z drewna. Głównymi procesami stosowanymi na skalę przemysłową jest proces wytwarzania ścieru klasycznego (SGW) oraz proces wytwarzania masy termomechanicznej (TMP) i chemotermomechanicznej (CTMP).
Ścier drzewny otrzymywany jest w procesie ścierania drewna na kamieniu pod ciśnieniem atmosferycznym. Drewno, z którego wcześniej usuwa się korę, jest rozwłóknianie za pomocą kamienia, a następnie obmywane wodą. Tak przygotowana masa osuszana jest w hydrocyklonach, skąd trafia do zagęszczarki. W kolejnym etapie gęsta masa drzewna trafia do kadzi magazynowej, a woda obiegowa (powstały filtrat) jest recyklowana z powrotem do ścieralni. Podczas produkcji ścieru z przerabianego drewna uwalniane są substancje żywiczne, które łatwo aglomerują i tworzą osady na ścieraku czy też ścianach wewnętrznych rurociągów. Powodują one często zanieczyszczanie powierzchni kamienia, co pogarsza jego właściwości ścierne. W celu zwalczania tych tzw. „trudności żywicznych” stosuje się różne środki chemiczne. Najczęściej stosowane są w tym celu dyspergatory, które mają za zadanie rozpraszanie powstających osadów, ułatwiając potem ich usunięcie. Doskonałymi dyspergatorami dedykowanymi przemysłowi celulozowo-papierniczemu są produkty serii ROKAcet i ROKAfenol. Oprócz swoich zdolności dyspergujących, produkty te mogą pełnić rolę środków czyszczących, emulgatorów oraz antyelektrostatyków. ROKAfenole doskonale sprawdzą się w procesach emulgowania i odplamiania masy papierniczej oraz celulozy. Z kolei ROKAcet R40W to środek o właściwościach zmiękczających, który może być wykorzystany w przemyśle włókienniczym, skórzanym i papierniczym.
Ulepszeniem SGW jest proces roztwarzania masy termochemicznej (TMP). W procesie TMP zrębki drewniane są początkowo myte w celu usunięcia piasku, kamieni i innych twardych zanieczyszczeń, następnie ogrzewane parą pod zwiększonym ciśnieniem, a dalej rozwłókniane w młynie tarczowym. W kolejnym etapie masa trafia do kadzi latencyjnej, gdzie następuje wyprostowanie i likwidacja odkształceń powstałych na włóknach. Finalnie jest ona kierowana do kadzi magazynowej. W celu zmniejszenia ilości szkodliwych żywic powstających w ścierze w technologii TMP stosuje się podobne środki chemiczne jak w procesie wytwarzania ścieru klasycznego. Powstała w ten sposób masa używana jest najczęściej do produkcji papieru gazetowego.
Proces CTMP łączy w sobie proces TMP wraz z chemiczną impregnacją zrębków. W pierwszej fazie są one myte i przesiewane, a następnie impregnowane. W zależności od rodzaju drewna stosuje się odpowiednie roztwory chemikaliów. Siarczan sodu jest zazwyczaj stosowany do drewna iglastego, natomiast do drewna liściastego najczęściej wybiera się zasadowe nadtlenki. Po skończonym procesie impregnacji wióry są ogrzewane i mieszane z wodą, która rozluźnia wiązania ligninowe i uwalnia włókna. Proces CTMP pozwala uzyskać czyste masy włókniste o dostatecznej wytrzymałości i odpowiednich właściwościach optycznych. CTMP jest głównie stosowany do produkcji włóknistych składników mas papierniczych, które mogą służyć do wyrobu papierów drukowych i higienicznych.
Flotacja i bielenie
Kolejnym etapem obróbki masy włóknistej jest odbarwianie połączone z mechanicznym usuwaniem zanieczyszczeń. W makulaturze stosowanej do produkcji papieru, najważniejszym parametrem jest kolor (tzw. białość w przypadku papieru drukowego). Z tego powodu makulatura musi być ona dokładnie oczyszczona z farby drukowej. Podstawowym warunkiem jej usunięcia jest uwolnienie cząstek farby z włókien i utrzymywanie ich w stanie zdyspergowanym. Tak rozdrobione cząstki tuszu są następnie oddzielane od zawiesiny włókien. Odbywa się to najczęściej na zasadzie różnic we właściwościach fizycznych materiałów, takich jak np. ciężar właściwy niepożądanych substancji w porównaniu z włóknami i wodą. Z racji tego, że większe zanieczyszczenia, takie jak np. części metalowe (zszywki) kamienie i piasek, są usuwane już na etapie rozwłókniania, bardzo często w stosunku do tak drobnych zanieczyszczeń stosuje się procesy flotacyjne.
Dodatkowym i często przeprowadzanym procesem jest bielenie. Stosowane jest w produktach wymagających wysokiej czystości, gdzie żółknięcie nie jest pożądane (np. papiery do pisania i drukowania). Bardzo popularnym środkiem wykorzystywanym do bielenia jest podchloryn sodu. Może być on także użyty do produkcji Karbometylocelulozy (CMC) z trocin. W tym procesie wykorzystywany jest także ług sodowy oraz kwas chlorooctowy (MCAA). Bielenie polega na zastosowaniu odpowiednich chemikaliów, które dodawane są bezpośrednio do dyspergatora w celu podwyższenia białości masy. Rodzaj zastosowanych włókien oraz pożądane właściwości końcowe produktu mają duży wpływ na stopień bielenia masy celulozowej. Masy zawierające materiały o wysokim zagęszczeniu są trudne do wybielenia i wymagają stosowania dużych dawek chemikaliów. Ścieki z instalacji bielących przed zawróceniem wymagają zastosowania szeregu środków chemicznych, które mają na celu zmniejszenie ich pienienia, korozyjności czy też obniżenie zdolności do powstawania kamienia. Produkty Grupy PCC, takie jak ROKAmery, doskonale nadają się do stosowania w procesach, gdzie pojawia się proces pienienia ścieków i wód technologicznych. ROKAmery to kopolimery blokowe tlenku etylenu i propylenu. Produkty te zmniejszają napięcie powierzchniowe pomiędzy cieczą a powietrzem, jednocześnie poprawiając „drenaż” piany, co w efekcie powoduje jej redukcję.
Finalne przetwarzanie masy papierniczej
Po zakończeniu procesów roztwarzania, flotowania i bielenia, gotową masę celulozową przetwarza się w masę papierniczą, którą następnie wykorzystuje się do produkcji papieru. Proces ten obejmuje kilka etapów:
- mieszanie masy celulozowej,
- tworzenie dyspersji masy celulozowej w wodzie,
- rafinację,
- wprowadzenie niezbędnych dodatków.
Dodatki używane są w celu wytwarzania produktów papierniczych o specjalnych właściwościach (tzw. papierów specjalnych) lub w celu usprawnienia procesu papierniczego. Najpopularniejszymi dodatkami są:
- żywice i woski do hydrofobizacji,
- wypełniacze, takie jak np. glinki, talk i krzemionka,
- barwniki nieorganiczne i organiczne,
- związki nieorganiczne poprawiające strukturę, gęstość, jasność i jakość druku (np. dwutlenek tytanu, siarczan wapnia i siarczek cynku),
- emulgatory i środki czyszczące.
Grupa PCC posiada w ofercie serię ROKAcetów stanowiących grupę produktów, które mogą pełnić obie te funkcje. Dzięki swojej budowie mogą być także wykorzystane w przemyśle papierniczym jako środki niskopienne i zmiękczające.
Poddana obróbce masa zostaje przetworzona na produkt papierowy za pomocą specjalnych maszyn. Po zakończonym procesie papier jest zwijany w rolę, która ma zadanie chronić go przed uszkodzeniami i zabrudzeniem. Do pakowania papieru najczęściej stosowany jest laminat PE-papier. Takie opakowanie zapewnia dobrą ochronę przed uszkodzeniami mechanicznymi, kurzem, a także wilgocią. Ogromną zaletą tego typu opakowań jest także to, że są one całkowicie recyklowalne, dzięki czemu mogą być ponownie przetworzone.