Plastics are a very wide range of products, including many products with different properties. The lack of detailed knowledge and familiarity with the use of their different types causes many people to simply refer to all such materials as plastic. Meanwhile, within this category, there are products and substances with very broad applications and equally different parameters. One of those with the widest and most universal use is polypropylene. What is worth knowing about it, what products are made of this material and why are they so popular? We invite you to read on!
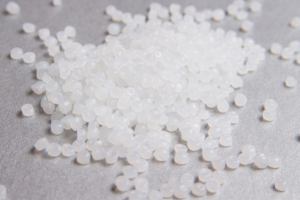
What is polypropylene?
Polypropylene (PP) is a chemical compound classified as plastic. It belongs to the group of polyolefins and is obtained in the process of propene polymerisation. Due to their extraordinary durability and hardness, polypropylene products are used in many sectors and industries.
Physical and chemical properties of polypropylene
As we have already mentioned, polypropylene is appreciated in many sectors of the economy due to its physical and chemical parameters. What properties of this substance are particularly desirable from an industrial point of view?
One of them is certainly the high chemical resistance to various types of compounds and substances. In particular, polypropylene is highly neutral to chemically aggressive acids, bases, and solvents. On the other hand, it is not resistant to non-polar liquids, e.g. benzene, methyl chloride, and carbon tetrachloride.
Another property of polypropylene is its low water vapour permeability. In addition to good insulation parameters, this material is also characterised by high air permeability and lack of water absorption. As a result, canisters, bottles, suitcases and various other products produced from it exhibit optimal resistance to moisture.
Polypropylene is also odourless and relatively easy to process. Especially the thermoplastic properties of PP make it a material of choice for manufacturing products of various shapes and sizes. After cooling down, the compound regains its original hardness. However, it should not be forgotten that it degrades at temperatures above 270°C.
It is worth adding that polypropylene products are made of polypropylene regranulate obtained in the recycling process (read also about upcycling). The constantly improving technology of PP production is definitelyan important step towards minimising the harmful impact of the chemical industry on the environment.
In which sectors of the industry is PP used?
A number of branches of modern industry use the above-mentioned advantages of polypropylene itself and the materials produced based on it. In fact, it would be difficult to find and identify those industries that do not utilise the potential of this universal, durable and safe material, even a little bit. The most popular, and the main areas of using PP in the modern economy include:
- food industry and production of packaging, where polypropylene is used, among others, for the production of bottles, containers and canisters, household items, carpets and even some toys,
- chemical and pharmaceutical industry, in particular the production of pipelines and conduits for the transmission of water and chemically aggressive media. In addition, PP is also used to produce laboratory vessels, filters, medical accessories and diagnostic equipment, disposable vessels and syringes,
- production of suitcases, containers, buckets and small tanks, e.g. for home sewage treatment plants,
- textile industry, including production of carpets, rugs, fabrics, synthetic fibres and certain tools,
- furniture and construction industry, e.g. insulation of building structures, bathroom fittings, cables in central heating and gas installations, production of furniture and furniture accessories,
- automotive industry, in particular the production of body parts, bumpers, mirror elements, cockpit fittings.
In addition, PP is used to produce, among other things, pallets and transport articles, swimming pools and small ponds, industrial casings, accessories for production machines, as well as electrical and electrotechnical articles.
ABS suitcases vs polypropylene suitcases
In recent years, we have observed a dynamic increase in the popularity of products manufactured from a different plastic, namely acrylonitrile-butadiene-styrene terpolymer, abbreviated to ABS. One of its basic advantages is its high resistance to mechanical stress, thanks to which ABS is often referred to as a hard or very hard plastic. Suitcases made of this material have become especially popular. Acrylonitrile-butadiene-styrene terpolymer is a hard material with a very low degree of elasticity. This means that with sufficient pressure, an ABS suitcase – even of the most prestigious brand – can simply break.
In the case of suitcases made of PP, this risk is minimal or non-existent. All because of the much higher elasticity. Polypropylene products are more flexible than those made of other plastics, which results in their better durability, even in difficult conditions. ABS is also more susceptible to scratches than PP, so when faced with the choice of a suitcase that will serve us for a minimum of several years, it is worth reaching for proven polypropylene products.
Heat-Set Technology
Another very interesting example of the use of PP is the production of synthetic fibres, which are an excellent alternative to natural wool. The mentioned material of animal origin is considered to be the best for the production of, among other things, carpets and rugs. There is a widespread opinion that only sheep’s wool carpet pile guarantees the highest comfort and a feeling of softness.
Meanwhile, synthetic carpets manufactured using the HEAT-SET technology are becoming more and more popular every year. What is this technology? It involves the use of improved polypropylene fibres, which in terms of durability, comfort and aesthetics, do not differ in any way from the natural hair of animals. Each of the single fibres used in the HEAT-SET method undergoes a process of thermal stabilisation. This opens up their ends, making the top layer of the rug fluffy and pleasant to the touch, perfectly imitating sheep’s wool.
PP bottles and canisters
The packaging industry also makes extensive use of the physical and chemical properties of PP, the best example of which are the canisters and bottles available on the market in a wide variety of shapes and capacities. It is polypropylene that is used to produce packaging with a capacity ranging from several dozen millilitres to several litres or more, used for storing, among other things, cleaning agents, disinfectants, cosmetics, chemical reagents, and some medications. Polypropylene-based plastics are also used in the production of canisters for storing and transporting fuels, as well as large barrels and industrial tanks. The latter are used to store ready-made substances as well as concentrates, and active substances, which are the main components of various types of chemical products, e.g. solvents, cleaning foams, and adhesives.
Corrosion inhibitors and the resistance of polypropylene
One of the reasons that PP products are so durable is the use of corrosion inhibitors, i.e. special substances that slow down or completely inhibit corrosive reactions in the production of plastics. Inhibitors protect metals and their alloys against biological, microbiological, galvanic, or crevice corrosion. As a result of the reaction with metal, an inhibitor, such as Chemstat CL-1020, forms a thin protective oxide film on the surface. This coating acts as a protective barrier against moisture and material deterioration.
Polypropylene products in the offer of PCC Group
Polypropylene has become such a widely used chemical material that today it is difficult to imagine individual areas of life without products made on its basis. PCC Group fully satisfies the needs of many modern industry sectors with a rich portfolio of both ready-made polypropylene products, but also various inhibitors, e.g. from the Chemax or Chemstat series, as well as ROKAmer emulsifiers and dispersants, used as additives to polypropylene and other plastics. The brand also offers polypropylene packaging and canisters, as well as a wide range of other solutions that fully meet the needs of the plastics manufacturing industries.
A wide variety of additives for plastics, such as thermal stabilisers, antioxidants, and lubricants, is a guarantee of optimal plasticity of polymers and their appropriate strength. We encourage you to get to know our wide range of additives for plastics, and contact us for detailed information about the parameters of individual semi-finished and finished products: containers, bottles, and canisters.