The corrosion of materials is a common phenomenon that cannot be entirely eliminated. Corrosive degradation is often classified as one of the main reasons of material loss. Additionally, it contributes to environmental pollution and is dangerous to human health. Learning about corrosion mechanisms and the methods of protection against material degradation allows us to safeguard the materials to a significant extent.
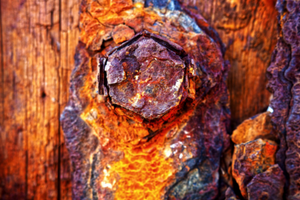
What is corrosion?
Functional items or architectural elements made of metals and their alloys are exposed to various environmental factors on a daily basis. This causes the degradation of materials due to chemical or electrochemical reaction, which is referred to as corrosion (chemical or electrochemical, respectively).
Corrosion is often called rusting, which refers to metal materials. When rusting occurs, a metal surface gets covered by the characteristic red tarnish called rust. Rust is not an individual chemical compound but a layer of oxides, hydroxides and ferrous salts (which are produced by the oxidation of iron and its alloys, such as steel).
Environmental factors causing corrosion:
- atmospheric precipitation,
- humidity,
- environmental pollution (e.g., sulphur oxides, nitrogen oxides, dust),
- inadequate pH level,
- material stress,
- presence of bio-organisms,
- contact with soil.
Chemical and electrochemical corrosion
Chemical corrosion
Chemical corrosion occurs in an environment where there is no ion conductivity, so usually in the presence of exhaust gases, petroleum, certain organic substances, or gases such as hydrogen, hydrogen sulphide, carbon monoxide (II) or chlorine. Chemical corrosion is sometimes called dry corrosion. Usually the entire surface of the corroding material comes in contact with the corrosive agent. This, however, normally does not pose a significant risk to the structure.
Electrochemical corrosion
It occurs in an environment capable of conducting electric charges (in electrolytes). An example of such an environment is water that includes dissolved gases or salts. In such a case, local galvanic cells (e.g., at the point of contact with moisture) are formed on the material surface. The presence of an electrolyte causes the circuit to close. Electrochemical corrosion results in oxidation on metal surfaces and the formation of a brown deposit (rust).
Metal corrosion and passivation
A metal surface that touches a corrosive agent is oxidised under its influence; it gets covered by a layer of metal oxide. This is not always undesirable. Passivation is a phenomenon where a sufficiently solid oxide layer is formed that is strongly bounded with the metal surface. It is supposed to protect the material against further degradation (further oxidation).
Passivation can be observed, for example, on aluminium. Although it is a high-reactivity metal, it shows resistance to corrosion, which is thanks to passivation. Metals are commonly subjected to passivation processes, as it is one of anti-corrosion techniques. However, passivation also exists in nature. It can be observed on copper, whose surface can be covered with a green tarnish called ‘patina’.
Is it only metals that get corroded?
Items made of metals or their alloys usually degrade due to chemical or electrochemical corrosion. The electrochemical corrosion of iron, steel, copper or aluminium is common, but it also affects other materials, not only metallic ones; for example, we can observe the chemical corrosion of concrete.
Materials (other than metals) that can corrode:
- concrete and reinforced concrete,
- plastics,
- wood,
- ceramics.
The corrosion processes for each material are different. Corrosion largely depends on the type of electric conductivity at the material/environment interface. Also the type of environment where the material exists is important. For bodies that feature high conductivity, we usually deal with electrochemical corrosion. In the case of low (or zero) conductivity, corrosion is much more chemical (or physico-chemical) in nature.
Anti-corrosion techniques
Corrosion cannot be entirely eliminated. All anti-corrosion techniques are aimed to inhibit that process. Precious metals that exist naturally in an unbonded form do not require anti-corrosion protection. These include gold or platinum.
Methods to protect against corrosion:
- eliminating the factors responsible for corrosion from the environment, for example eliminating moisture, using ion exchangers to remove salts dissolved in water, neutralising acidic substances;
- using substances that slow corrosion down (inhibitors);
- changing the metal’s electric potential;
- using protective coatings. A metal can be covered with another metal more precious (insulation coating) or less precious (shielding coating) than the one being protected;
- using non-organic coatings, e.g., vitreous enamels, chromate coatings;
- using organic coatings, e.g., polymer materials or topcoat paints.
Coatings are a popular anti-corrosion protection. They are applied by submerging the item in a molten metal (hot dip coating) or taken from an aqueous solution of electrolyte, through electrolysis electrolytic coating). A less popular method is metal spraying, which is carried out with a spray gun.
The most popular protective metal is zinc. It is used especially as a coating for steel or cast iron. A zinc coating shows good protective properties despite its lower thermodynamic stability compared to iron. However, while protecting the metal item against degradation, the zinc itself may corrode when exposed to moisture. The durability of a zinc coating depends not only on its thickness but also on the environmental conditions in which the item is used. Based on the method of application, we either electro-galvanise or hot dip galvanise
Economic effects of corrosion on a global scale
Corrosion is a global issue. We keep recording injuries and deaths, economic losses and negative environmental effects caused by the corrosion of materials. Corrosion may lead to serious failures in pressure tanks, aircraft components and traction equipment.
As Mohmmad A. Jafar Mazumder indicates in his article titled Global Impact of Corrosion: Occurrence, Cost and Mitigation (2020), the typical maintenance cost of corrosion-related issues for a particular country varies from 1–5% of its gross national product. In 2013, NACE International conducted a global study on the economic impact of corrosion. Among other things, it was aimed at showing how important it is to integrate anti-corrosion technology with management systems. According to the published report, the cost of corrosion is estimated at $2.5 trillion, that is 3.4% of global GDP, which means that every year countries all over the world have to budget significant amounts for combatting corrosion.
Sources:
https://irispublishers.com/gjes/fulltext/global-impact-of-corrosion-occurrence-cost-and-mitigation.ID.000618.php
https://psk.org.pl/aktualnosci/ekonomiczne-skutki-korozji