In the recent years, the demand for batteries, in particular lithium-ion batteries, started to exceed the supply. Their global availability is becoming a strategic asset that determines competitiveness and development in a growing number of economic sectors, for instance in power tool manufacturing or in energy storage systems. The manufacturing process of lithium-ion cells is complex and depends on a range of factors, the most important being the quality of the raw materials used for production, sustainable development goals, and the possibility to increase production capacity.
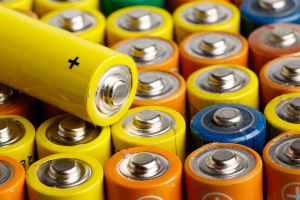
The structure and operating principle of batteries
Batteries produce electric energy though the chemical reaction occurring inside the cell. The key to carry out that reaction is the motion of electrons. Electrons are negatively charged particles that generate electricity while moving. This flow is possible with the use of two different metals acting as conductors. Wiring the metals together initiates the motion of electrons between them, which is caused by the electrons being pulled by the metals that are referred to as cathode and anode. Electrons will always be pulled stronger by the cathode. The metals inside a battery are interconnected by a substance capable of conducting electrons, called the electrolyte.
Electric vehicles use batteries built of interconnected cells. The power systems used are different from one another mainly by their useful life, chemical composition, and weight. The market of electric vehicle batteries is changing dynamically. Presently, lithium-ion batteries are amongst the most popular types. Their production is complex and requires top quality at each stage. The most popular lithium-ion batteries are those whose cells are based on such metals as nickel, cobalt, or manganese. The types of lithium-ion batteries most commonly chosen for electric vehicles include lithium-nickel-cobalt-manganese (NMC) batteries. Lithium-manganese (LMO), lithium-iron-phosphate (LFP) and lithium-nickel-cobalt-aluminium (NCA) batteries are of much lower interest.
How is a battery made?
Manufacturing of lithium-ion and other cells is characterised by its complexity and a high degree of automation. The production of batteries depends on their type, but the principal stages and processes are similar. To put it simple, the entire manufacturing process can be divided into three main “blocks”:
1. Electrode production
Regardless of the format and shape of the battery being produced, the first step is to make the electrodes. At this stage, it is important to avoid cross-contamination between different materials, so in practice there is a separate line for producing the cathode and a separate line for the anode. The anode is produced from copper foil covered with graphite, while the cathode is made from aluminium foil coated with a selected metal. The most important production phases include:
- Mixing, which consists in producing the so-called suspension that is a mix of powders (active substances) with a solvent, and other chemical substances that act as binders.
- Coating and drying: a ready suspension is pumped into the coating area, where it is applied on a metal foil. The foil is then sent to a drying stove, where the solvent evaporates and the active substance is being attached to the foil.
- Calendering – the process of finishing the coated rolls. They are moving between two heated elements that provide appropriate compression of the material by pressing the rolls against the foil and thus maintain a stable thickness and density and a better adhesion.
- Cutting – the metal foil runs though a system of knives that cut it into many smaller pieces whose sizes are suited to the electrodes to be produced.
2. Cell assembly
The assembly of cells requires a dry environment in order to prevent the formation of moisture that can cause degradation and a significant drop in efficiency of the electrode. At this stage, the electrodes are cut and placed in casings. Cell assembly covers the following steps:
- Cutting – rectangular electrodes are produced during the cutting process. The cutting is performed mechanically or with a laser.
- Arranging – in a battery casing, electrodes are arranged alternately: anode, separator, cathode. The most popular way is stocking.
- Assembly – appropriately arranged electrodes are connected and attached to the main clamps by welding. The so produced cell with electrodes is placed in packaging material and sealed, leaving an open edge for filling with electrolyte.
3. Forming and quality control
Then an assembled battery goes through the conditioning phase. This is often a critical moment of production, as the cell is charged for the first time and undergoes a range of tests that are to prove its quality and efficiency. The final stages of forming a battery include pre-charging, degassing, and ageing at a high temperature. When that last phase is finished, the device is ready for use in different applications.
Electric vehicles are powered by lithium-ion batteries. They are among the most popular types of batteries, mainly due to the fact that they allow for driving more miles on a single charge compared to other battery types. Their manufacturing process is very similar to that of the most common lithium batteries. A characteristic feature of electric car batteries is that they constitute a series connection of several lithium-ion cells that compose so-called modules. Each module of a battery contains a few to more than ten cells connected in series. Then the modules are welded together to form battery packs that undergo quality control.
Raw materials for battery production
The most popular energy storage systems include lithium-ion batteries. The production of these cells is complex and requires top quality at each stage. An important issue is to choose such raw materials for production that the finished battery can fully address market demand and consumer requirements.
Metals
The most important raw materials for battery production include metals, mainly lithium, cadmium, nickel, iron, zinc and manganese. The latter is the most popular material used to produce lithium-ion batteries. Other elements used for battery production are magnesium and aluminium (as electrodes), due to their high standard potential and electrochemical equivalent. An additional benefit is their relatively low price and high availability. This makes them an ideal substitute for popular electrodes made of zinc. Another metal applied in batteries is silver, which allows for producing safe cells with a high energy density. Additionally, the use of silver makes it possible to achieve higher battery voltage compared to cadmium, for example.
Metal oxides
Electrodes in batteries (cathodes and anodes) are not only made of metals. Metal oxides, such as manganese (IV) oxide or zinc oxide, are also used. The active material in lithium-ion batteries is usually lithium, which most commonly occurs in the form of oxides combined with such metals as cobalt, manganese, nickel, vanadium or iron.
Electrolytes
The electrolyte is the key component of lithium-ion batteries that enables a free flow of electrons between electrodes. Electrolytes are principally aqueous solutions or solutions in organic substances, which are produced by solving one or more types of salt, for example ammonium chloride, zinc chloride or magnesium perchlorate. In alkaline batteries, potassium hydroxide is used as the electrolyte. Vinylene carbonate is also commonly selected for producing electrolytes for lithium-ion batteries. It is particularly important for the dynamically growing sector of batteries and accumulators. High-purity vinylene carbonate (minimum 99.99%) is available in the broad product range of the PCC Group, which is one of the leading manufacturers and suppliers of chemicals and raw materials for any industry.
Graphite
Graphite or powdered carbon is a key raw material for electrode production. The structure of some batteries includes graphite bars that “collect” the electrons inflowing from the circuit and distribute them across the cathode. In addition, the structure of graphite facilitates the extraction of gases produced during an electrochemical reaction.
Plastics
Plastics, such as polyethylene or polypropylene, are excellent materials that are applied in the production of battery separators. They separate the cathode from the anode. Plastics are also used to make coatings and casings for batteries.
- https://www.discoveryuk.com/how-its-made/how-are-batteries-made/
- https://academic.oup.com/bcsj/article/95/1/195/7226594
- https://www.madehow.com/Volume-1/Battery.html