Inks are materials usually in liquid form, used for writing or printing. Their main application is to stain the surface to obtain a text, image or pattern.
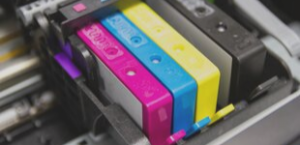
Furthermore, the inks must have the appropriate technical parameters. It is crucial that they are dried in the appropriate conditions for the given process, and also have certain strength properties, depending on the final use of the given printed material. Other important printing properties are: the plasticity of the paint, the susceptibility to delamination and its thixotropy, i.e. the ability to change the viscosity, e.g. under the influence of mixing.
Application and properties of the inks
The inks are extremely versatile and can be used on virtually any surface, regardless of its texture, size or shape. They can be used in the colouring of paper, plastics, metal, glass and textiles. Printing inks, unlike paints and varnish coatings, are applied to the surface in the form of a very thin layer, which, depending on the printing process, may have a thickness of 2 to 30 μm. The visual characteristics of the ink depend on three main factors, namely: its colour, transparency and gloss. In addition, several features that are interrelated with each other, influence the colour of the ink. The colour depends also on the intensity and saturation, and its purity informs us how dark or light the ink will be.
Of course, the chemical structure of a dye has a key impact on its shade, particle size or the ability to apply a given ink. It is the use of different types of resins, oils and solvents that affects the hue or purity of a given dye. Sometimes, even some additives (e.g. for dispersion) can cause changes in the colour of the paint. In addition to the structure of the ink itself, the proportions of its individual components are also very important.
Components of printing inks
The main components of the printing ink are:
- Colouring substances – they constitute from 5 to 30% of ink. They are usually pigments, dyes or lakes. Pigments are finely shredded solid substances that do not dissolve in the binder, but are dispersed in it. While dyes are substances that are completely soluble in the binder. The last colouring substance is lake. These are dyes precipitated from the solvent to a solid form, which thereby acquire properties similar to pigments. Typically, it can be observed that a higher concentration of a specific dye affects the intensity of its colour. In practice, however, optimal concentrations of colouring substances are used, above which no change in the colour is noticed.
- Binder – constitutes from 15 to 50% of the composition of the ink. It is designed to wet the pigment, which facilitates the dispersion of its particles. It is the adhesive that determines the printing properties of the ink, as well as the way it binds with the substrate. These substances additionally provide adequate gloss and wear-resistance. Usually various types of resins are used as binders. The PCC Group offers a range of products that are used as intermediates for the preparation of base resins. They are then mixed with appropriate additives to obtain the final ink. These products include Rokopol® D2002 and Rokopol® LDB series (2000D, 4000D, 8000D and 12000D). As the molecular weight increases, they become more and more hydrophobic, and their reactivity decreases. This allows you to choose the right composition depending on the expected final parameters of the ink. In addition, Rokopol® products can be used as intermediates to connect reactive functional groups used in other technologies than polyurethane,
- Solvents – these are substances that are designed to dissolve the binder and mix with the other components of the paint. The diluent is typically 15-65% of paint composition. Due to its chemical properties, dichloropropane (DCP) works great as a solvent in printing inks. It is a colourless liquid without mechanical impurities with a characteristic odour. DCP can successfully replace organic solvents such as toluene, acetone and other xylene derivatives, at the same time it has a stable price,
- Excipients – affect the usable properties of the paint. Usually, they do not exceed 10% of the composition. The EXOdis PC30 product can be used as a dispersion additive for all kinds of water-borne paint and printing inks. EXOdis PC30 provides excellent final stabilization of dye products even in small concentrations. In contrast, the products ROKAdis 900 and ROKAdis 905, in addition to their dispersing capabilities, are also excellent wetting agents. For this reason, they can be used in the production of printing inks and inks, ensuring proper dispersing of pigments that are components of colorants,
The most popular printing techniques
In practice, the composition of the printing ink and its physical appearance depend mainly on the printing technique that we use:
- Flexographic and intaglio printing. The inks used for this type of print are characterized by a very smooth consistency, which is why they are colloquially called liquid connectors. Due to their excellent fluidity it is possible to use highly volatile solvents, thanks to which these inks dry very quickly. Initially, natural rubber was used in the production of this printing form. Then it was replaced with nitrile and butyl rubber, and currently the most widely used are photopolymers. The layer thickness of these paints applied to the surface usually does not exceed 10 μm,
- Lithographic paints and typographic prints. The inks used for lithography and typography are very sticky and resemble more paste than liquid in their consistency. For lithographic and typographic printing, non-volatile solvents are used so that they do not evaporate during the printing process. The main carrier of these paints are pigments and lakes, and the binder is usually resins or modified mineral oils,
- Screen printing inks. The inks used for this type of print are similar in their texture to paints. Screen printing provides greater versatility than traditional printing methods. Screen printing inks can be used to work with various materials, such as textiles, ceramics, wood, paper, glass, plastics and many more.
Drying of the printing inks
Often the inks are divided in groups based on their ability to consolidate. Printing inks in their base form are liquid or very similar to liquid form. Their change from liquid to solid state is called drying of the ink and can be carried out using physical or chemical methods, or as a combination of both. There are several types of drying:
- Absorption drying. The ink is dried when it passes through the fibers of the surface and also when it is absorbed by the surface itself.
- Oxidation drying. The ink dries due to the oxygen absorption process from the atmosphere. The gas chemically combines with resins and changes their physical state from liquid to solid. The oxidation drying process is quite slow and lasts up to several hours. It is influenced by a number of factors, e.g. the type of pigments and additives used.
- Evaporative drying. This is the type of drying that depends on the evaporation rate of selected solvents, as well as the affinity between the resins and the solvents used. In practice, the higher it is, the more slowly it evaporates. The affinity between resins and solvents used in the ink also affects its properties. This has a direct impact on the ability of printing, the speed of the entire process of drying and retention of solvents in the layer of ink.
- Chemical drying. This process strongly depends on what types of chemical compounds we are dealing with. Some systems may contain, for example, a polymerizable compound that requires a catalyst to effect a given chemical reaction. Or in other option, it may be necessary to provide heat to the process to initiate a chemical crosslinking reaction. Each of these processes requires specific conditions in which chemical reactions will take place.
- Radiation induced drying. This type of drying can be divided into several groups: drying using ultraviolet radiation, infrared, electron beam or radio waves. Each of these methods is determined by the chemistry of the ink carrier and the type of ink itself. Ultraviolet drying uses a process called photopolymerization. The inks contain photoinitiators that initiate a chain reaction with the ink carrier during the drying process. Then a rapid polymerization process takes place and the state of the fluid changes to a highly cross-linked solid, colloquially called a film. Electron beam drying is very similar, and the difference consists in using high energy electrons for the process, which generate free radicals, leading to rapid polymerization of the paint carrier. The last type of radiation induced drying is the use of radio waves. This type of drying is used when the inks contain a large volume of polar molecules, e.g. water. Radio radiation is absorbed by polar particles, which causes very rapid heating of the paint.The water then evaporates and a thick layer of ink is obtained.
Trends in the printing industry
The printing market is constantly changing. Based on the Ceresana report, its value is estimated to reach $ 25.7 trillion by 2023. Such a large increase in recent years is caused by the growing popularity of digital printing. The digital printing process is much faster and more efficient than traditional printing methods. The popularity of digital printing is also due to the changing needs of consumers. In regions where there has been a significant increase in digitization, a noticeable decline in the collections of newspapers, magazines and books can be observed.
The popularity of digital printing is also caused by the increasing demands placed on printing plants. The tendency to reduce the number of printouts, and on the other hand, an increasing number of print orders and the personalization of content, favour the use of digital printouts. In addition, digital printing allows substantial time savings, thanks to accelerated production and easier adaptation depending on the order. Digital printing systems also have an advantage over traditional printing when it comes to printing advertising materials or labels. What’s more, continuous technological progress constantly increases the print quality and speed of the process, which directly translates into cost savings. For this reason digital printing is becoming competitive and cost-effective in many fields.
Within the printing industry, an increasing ecological awareness can also be observed, which leads to the continual development of modern printing inks and methods of processing. It is estimated that in the coming years UV-curable inks and other radiation methods will gain in importance. There is an increasing use of such modern products, of course at the cost of using traditional solvent-based inks. Cerasana analysts estimate that the use of UV-curable inks will increase by over 13% in the coming years.