Reforming is a process that consists in the conversion of hydrocarbons with simple chains into hydrocarbons with branched chains or rings. It is a reaction that is usually aimed at producing fuel with a high octane number from light fractions of crude oil or cracking products. Among these products, we can distinguish motor petrols and hydrocarbons containing aromatic ring(s); it is usually the BTX, which is a mix of benzene, toluene and xylenes. The reforming of petrol entails many special reactions: dehydrogenation of naphthenes, dehydrocyclisation of paraffins, hydrodealkylation of alkyl-aromatic hydrocarbons, hydrocracking, and paraffin isomerisation. The reforming process delivers appropriate ingredients required to compose fuels. At the same time, the process produces hydrogen gas that is a valuable reagent during hydroprocesses such as hydrorefining or hydrocracking.
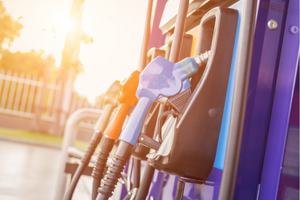
Octane number
The indicator that defines the anti-detonation properties of the fuel used to drive combustion engines with spark ignition is called octane number. In practice, it is a conventionally determined resistance of fuel to engine knocking, which involves an abrupt growth of burning rate. Octane number is enumerated by comparison. Resistance of the tested fuel to detonation combustion is compared with the resistance shown by standard mixtures that contain n-heptane and isooctane. To a certain extent, it is a sort of a fuel quality scale. Isooctane reflects the best classes, i.e., the fuels with the most desirable combustion, so its octane number is 100. Only fuels with a 100% content of isooctane, or equivalent mixtures, have such a high rate. Meanwhile, n-heptane is the opposite point on the scale, so both that compound and mixtures being identical in terms of combustion have an octane number equal to 0. A great example are the most popular fuels that we can find at petrol stations. The fuel designated as Pb97 is nothing but a mixture containing 97% of isooctane and 3% of n-heptane. It may also be other compounds, but they always have to correspond to those hydrocarbons in terms of the ease of combustion and maintain the same proportions in the mixture. Similarly, the petrol with index 95 contains 95% of isooctane and 5% of n-heptane (or a similar substance). This is why it is called 95-octane or 98-octane petrol.
The history of reforming
Reforming practices have been applied in the industry since the 1930s. To obtain a better-quality petrol and aromatic compounds, reforming was carried out at very high temperatures (510–590 oC) and under a pressure of 5–7 MPa. At the same time, a method using catalysts was being developed. In Germany, they developed a cyclically regenerated, fixed-bed catalyst having the form of molybdenum oxide set on aluminium oxide (MoO3/Al2O3). In the U.S., they used a non-regenerated, fixed-bed platinum catalyst set on aluminium oxide (Pt/Al2O3). Since 1952, its role in the United States has been taken over by a new fixed-bed catalyst: platinum on an aluminium silicate carrier (Pt/SiO2•Al2O3), which outclassed its predecessor with the possibility of periodic regeneration. In 1955, for the first time they used entirely new approaches that involved the mobile phase of the catalyst Cr2O3/Al2O3, which was subjected to continuous regeneration, and the catalyst MoO3/Al2O3 in a fluidal system, also with continuous regeneration. In following years, related reforming methods were developed that included the new bimetallic polymetallic catalysts applied on carriers. These included in particular Pt-Re, Pt-Ir and Pt-Sn. Only such combinations ensured the desired stability and selectivity of the process.
Raw materials used in reforming
Direct raw materials in the reforming processes are low-octane chemical compounds acquired by distillation of heavy petrol and other raw materials with boiling points ranging from 60 to 190 oC. Due to the restrictions related to the content of benzene in petrols, the applied raw material should not show the presence of benzene precursors such as naphthene C6. This implies that the boiling point of the relevant raw material should not be lower than 85 oC if the goal is to produce potential fuel composites. The most desirable characteristics of raw materials also include the content of aromatic hydrocarbons being lower than 20%(v/v), and the aggregate value of naphthenes and aromas being higher than 60%(v/v).
The process of reforming
The most important parameters necessary to initiate the reforming process are high temperature and pressure. Presently, the most commonly used conditions include a temperature of 480–550 oC and a pressure of 0.7–3 MPa of a hydrogen-rich gas, and the use of catalysts. These usually contain 0.3–0.37% m/m of platinum as well as small amounts of rhenium, iridium or germanium, which are the so-called bimetallic / polymetallic catalysts. The petrol and kerosene fractions whose boiling point is lower than 190 oC are usually subjected to preliminary hydrorefining, which allows for removing any compounds that cause the catalysts to deactivate. High process temperatures and contemporary specialised catalysts initiate the isomerisation of simple, aliphatic hydrocarbon chains to branched aromatic structures. Isomerisation entails dehydration of the hydrocarbon present in the raw material, followed by its chemisorption on metallic centres. This results in the formation of naphthene hydrocarbon, from which hydrogen separates, with transformation to the appropriate aromatic hydrocarbon that undergoes cyclisation. Paraffins present in the raw material may undergo slow hydrocracking, while olefins (undesirable at high concentrations) transform into isoparaffins by hydroisomerisation. From that form, subsequent cyclisations may occur. Naphthenes exist in the form of cyclopentanes and cyclohexanes at 18–50%, with the former ones prevailing. The latter compounds undergo dehydration to produce aromas. As with most reactions that occur during reforming, it is an endothermic and reversible process. Cyclopentanes undergo complete dehydrocyclisation with the production of aromas. The dehydrocyclisation of alkylpentanes is a multi-staged process that includes: dehydrogenation to cycloolefins, isomerisation from five- to six-segment cycloolefins, hydrogenation to naphthenes, and dehydrogenation to aromatic hydrocarbons. An example of such a cycle of transformations can be the chain al. methylcyclopentane – methylcyclopentene – cyclohexene – cyclohexane – benzene. Since all process (except isomerisation) performed during reforming are endothermic, an increased temperature and low pressure favourably affect that procedure. To prevent the depositing of reforming coke on the catalyst, and thus its deactivation, an increased hydrogen pressure is used.
The products of reforming
The immediate products of reforming include a raw reformate whose octane number grows to approx. 90 relative to the raw material, as well as liquefied petroleum gas and hydrogen. To improve the quality of reformate, it is purified by washing with a solvent, which results in the formation of raw petrol. This, in turn, is enriched by adding appropriate components.
Sources:
https://encyklopedia.pwn.pl/haslo/reforming;3966646.html
https://www.naukowiec.org/wiedza/chemia/reforming-izomeryzacja-_1190.html
Z. Sarbak „Reforming katalityczny”